Use of an Emec dosing station in a dairy for dosing acidic cleaning agents
In a dairy, a dosing station for acidic cleaning agents is used for the precise, automated mixing and dosing of acidic cleaning agents that are used in the cleaning and disinfection of production facilities. The dosing and application of acidic cleaning agents is particularly important here, as milk residues contain minerals and often cause limescale and protein deposits, which acidic cleaning agents can effectively remove.
In this particular application, an Emec dosing pump station was installed, which is controlled by a higher-level control system and ensures the continuous dosing of acidic cleaning agents into the application process. For safety reasons, the dosing cabinet was equipped with an additional leakage probe. Three Emec Prius D dosing pumps with a capacity of 240 litres per hour were installed in the dosing station.
The general workflow and functionality of such a dosing station is described below using a dairy as an example.
- Storage tank and acid detergent
- The acid detergent is kept ready in a storage tank.
- The storage tank is usually large enough to ensure continuous cleaning and maximise the efficiency of the cleaning process.
- The dosing station is often equipped with sensors that monitor the detergent level and sound an alarm when the level is low.
- Dosing pump
- A dosing pump ensures that the correct amount of acidic detergent is dosed into the water or into the cleaning process.
- This pump can add the detergent precisely and in coordinated quantities to the water flow.
- The dosing quantity and concentration can be adjusted based on the type and quantity of soiling and the specific requirements of the cleaning step.
- Mixing chamber
- The acidic cleaning agent is mixed with water in the mixing chamber.
- This ensures a uniform concentration to achieve an effective cleaning effect.
- The temperature of the water is often controlled, as the efficiency of cleaning can increase with higher temperatures.
- Control and monitoring
- The dosing station has a control system that monitors the dosing quantity and frequency.
- In modern dairies, these systems are usually automated and connected to a central process control system.
- They monitor and document the cleaning processes and report deviations or problems that could lead to interruptions or ineffective cleaning.
- Cleaning circuit
- The mixed cleaning agent is pumped through a circuit that runs through various system components (e.g. pipes, tanks, pasteurisers).
- During this process, milk residues, minerals and biofilms are dissolved and removed.
- The circuit usually ends in a return system in which the detergent is returned for disposal or reprocessing.
- Rinsing
- After the acidic detergent has been used, the entire system is thoroughly rinsed with water to remove detergent residues.
- This is particularly important to ensure that no residues end up in the subsequent dairy products.
Benefits and importance in the dairy
- Efficiency: Automation reduces labour costs and ensures consistent quality.
- Accuracy: Precise dosing minimises chemical consumption and protects the system from damage caused by excessive concentrations.
- Hygiene: Acidic cleaning agents effectively remove mineral and biological residues and prevent the formation of deposits that could favour bacterial growth.
These dosing stations play a central role in hygiene assurance and quality assurance in dairies.
We would be happy to advise you on the use of an Emec dosing station in your application.
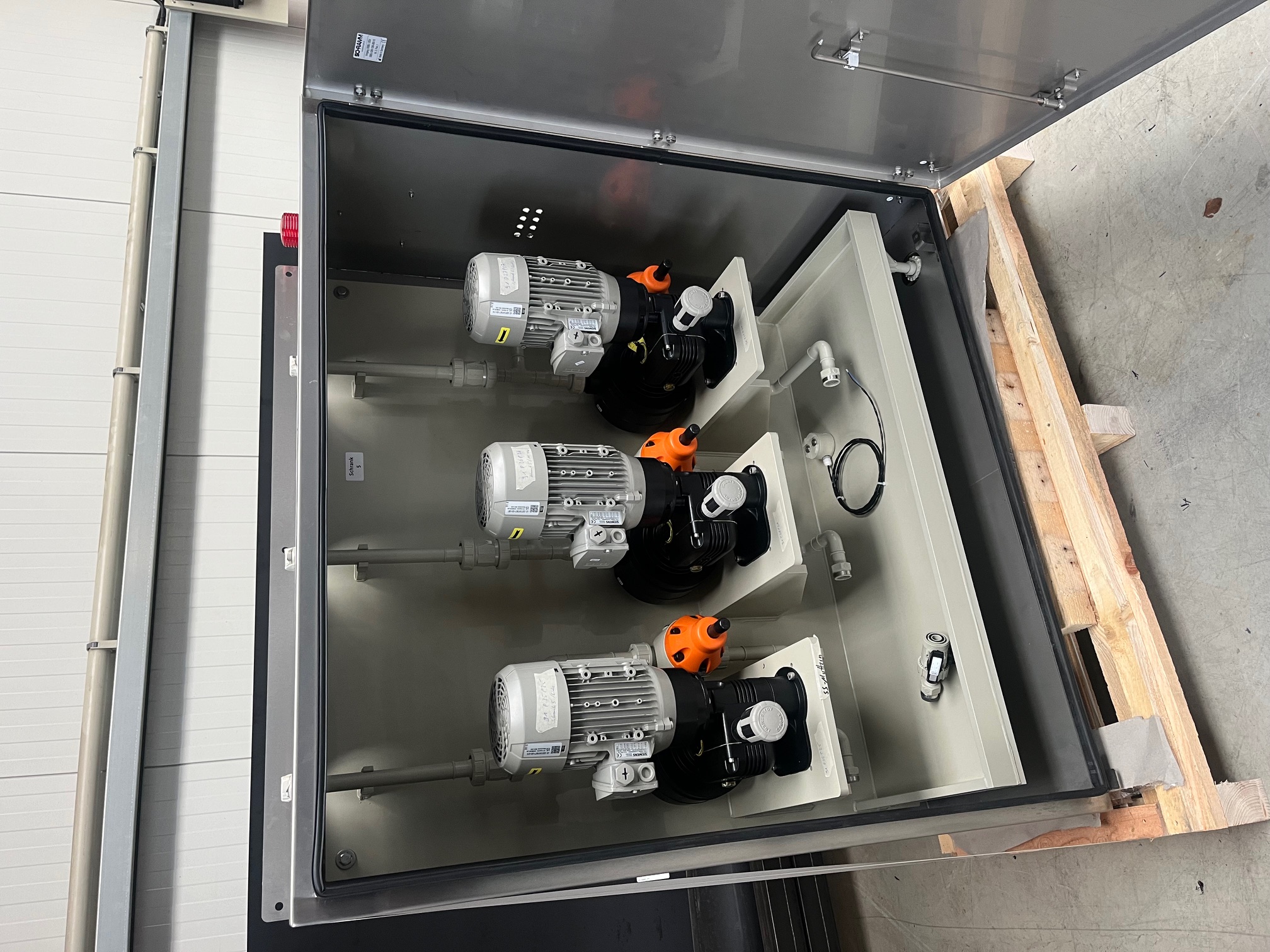
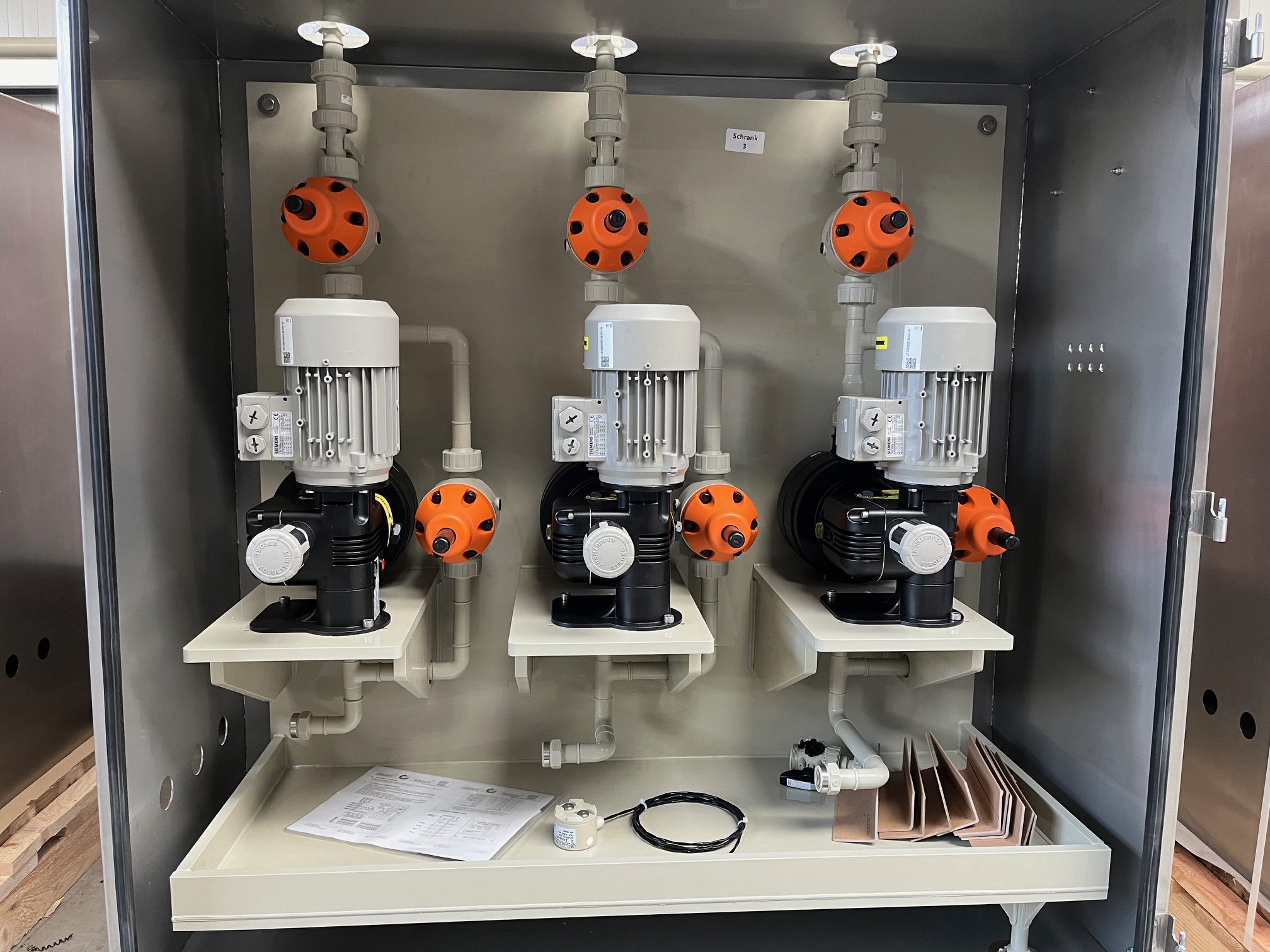